提到傢具廠,首先給人的印像是轟鳴的機械聲、粉塵、油漆味,但走進四川亞度傢具有限公司5G+智慧定制車間,將徹底顛覆你的認知。車間整體環境乾淨整潔,沒有嘈雜、轟鳴的機械聲,沒有粉塵與濃厚的油漆味兒,一台臺智慧化設備正按照圖紙智慧化施工,車間內的十余位工人在生産線上僅充當“配角”。
這樣的變化,源自於該公司開展的智改數轉。四川亞度傢具有限公司技術總監季雷介紹,傢具製造業是一個比較傳統行業,也是一個勞動密集型行業。隨著近年消費者需求的變化,以及定制傢具的快速發展,傳統的傢具製造業迎來了新挑戰。
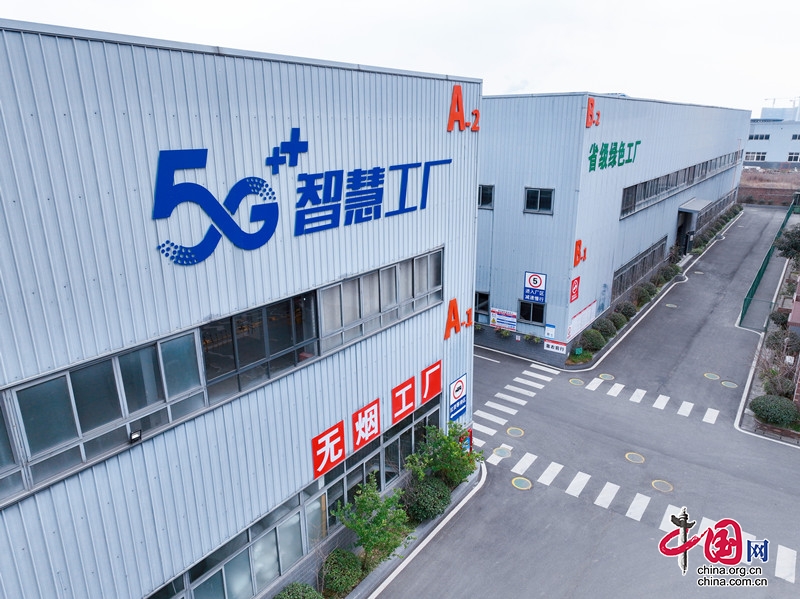
“每個消費者的需求不一樣,每一套定制傢具的數據、模型等都不一樣,如果還是按照傳統的生産模式,成本高效率也低。”為了適應市場變化,2017年,亞度傢具開始自主研發數字化系統,將5G與工業網際網路深度融合,2019 年成功上線國內首個完全自主智慧財産權的木質傢具行業工業網際網路平臺。在這個平台中,每個産品、設備和零部件都被賦予了唯一的標識,實現了資訊的互聯互通和實時共用,不僅提高了生産效率,還降低了物料損耗和運營成本。
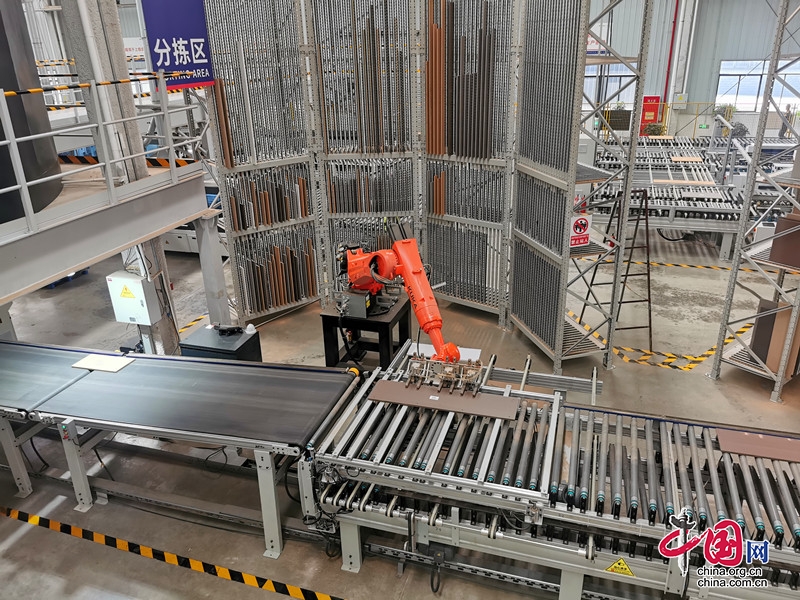
走進該公司智慧定制車間,沿著傳送帶向前望去,能夠看到板材結束加工後,會被傳送到一排紅色機械手面前。通過智慧識別,機械手會自動抓取産品進行歸類。歸類後,板材將自動傳送到包裝處,工作人員打包後,由藍色的智慧小車自動運送到立體式智慧倉儲車間,歸類碼垛……一系列操作行雲流水,智慧化貫穿了整個流程。
“現在我們的生産週期由30天縮短到3天,生産效率大幅度提升。”季雷進一步解釋,在産品設計上,通過工業網際網路雲設計平臺,實現前端設計和後端製造數據模型一體化協同研發。製造環節上,通過人機料法環全要素數據分析和智慧決策,使訂單交付週期從35天縮短至15天,綜合製造成本降低30%。供應鏈管理上,推行基於數據的計劃協同和並行決策,以智慧揉單實現拉動式生産,對各環節進行齊套智慧分析,優化生産資料配置。截至目前,公司庫存週轉率提升230%,庫存成本節省5000萬元。
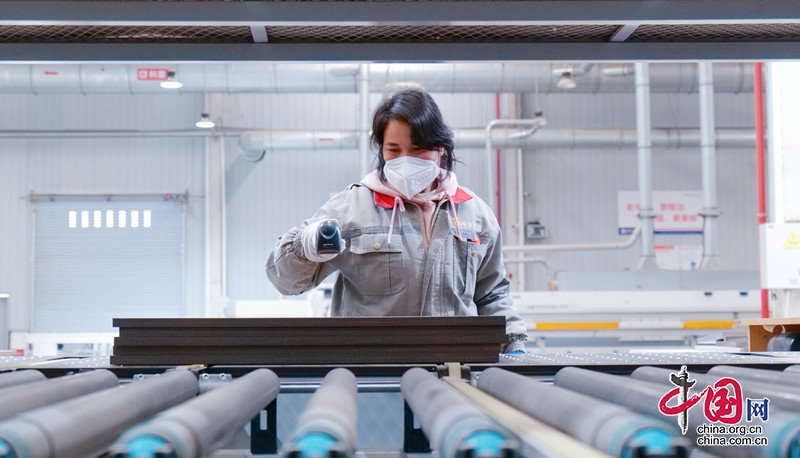
截至目前,該公司已累計投入資金超2億元,建設5G智慧工廠1座,引入智慧産線5條,搭建工業網際網路平臺3個、標識解析創新應用平臺1個,覆蓋智慧家居、智慧養老、商用辦公等綠色傢具産品,包含産品設計、智慧排産、智慧製造、供應鏈協同、售後服務等80余個應用場景。亞度傢具也被認定為工業網際網路領域的創新領航者,成為了四川省“專精特新”企業。
亞度的轉型升級,為其他傳統傢具企業推進數字化、資訊化轉型提供了新思路。目前,該公司已開展為産業鏈提供智慧改造和數字化轉型服務,在全國範圍內已服務173家産業鏈上下游企業,實現協同供應、設計和製造三個板塊的協同發展。(張漁)